
Standardisation of Wind Turbines
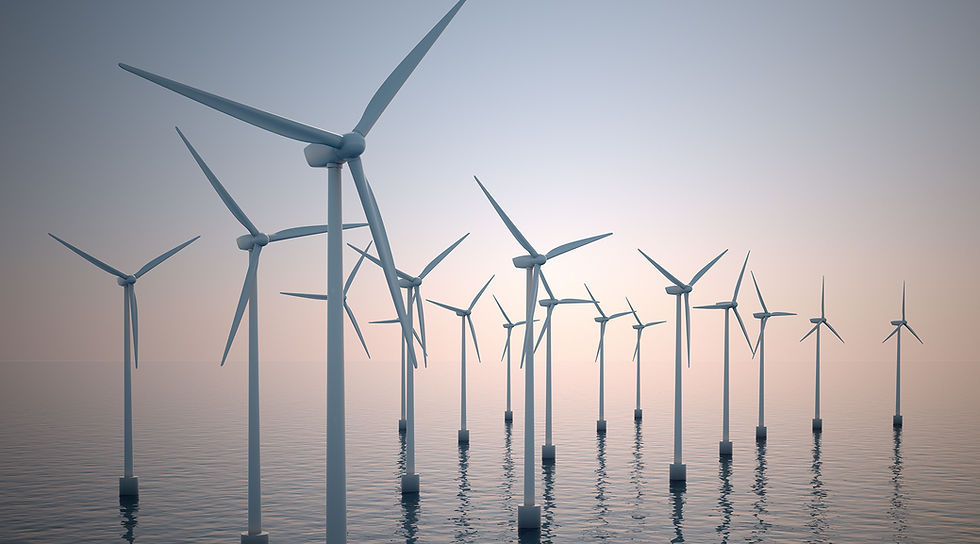
Released on March 23, 2021 by Leandro Soares da Costa, Director at Tupi Energy
Products standardisation has been adopted in the energy industry as an important engineering design technique. Its benefits have simplified project management processes, improved production and the marketing approach, making it an attractive business strategy for many organisations. Moreover, the design of standardised components reduces manufacturing and procurement costs; minimises delivery time; and optimises testing, installation and maintenance procedures.
These techniques have been commonly used in the design of wind turbines. The table 1 presents examples of onshore wind turbine models that are developed by three of the largest manufacturers: Siemens Gamesa, GE Renewable Energy and Vestas. The strategy used in the development of such standardised models is defined mainly based on the nominal power capacity of each wind turbine, environmental conditions and legal requirements.
Table 1 – Onshore Wind Turbine models developed by Siemens Gamesa, GE Renewable Energy and Vestas

The design and configuration of wind farms is specified in agreement with the power demand in terms of total capacity and where the project is being executed. Standardised wind turbines units have been installed, for instance, in Trøndelag, Norway, as part of the Fosen Vind project’s scope. With an estimated total capacity of 1.057 GW , this project comprises the installation of 278 onshore wind turbines developed by Vestas, of which 248 and 30 are models V117-3.45MW and V112-3.45MW, respectively .
Most components of a wind turbine can be standardised for optimisation purposes. Parts as blades and tower are manufactured through processes that utilise sealed mold. The standardisation of these items reduces the manufacturing cost, since the mold can be reused in several projects. Other mechanical and electrical components which are part of the gearbox, shafts, brake, rotor, yawing system, generator and controller, can be procured on a large scale if standardisation processes are adopted, reducing the supply chain costs and optimising testing, installation and maintenance activities.
Although standardised processes may affect innovative developments, the design of “off-the-shelf” products is still widely adopted by wind turbines manufactures. The ideal business model should be the one in which standardised and customised processes are implemented. Thus, customers’ requirements are met and new technologies are deployed.
References:
(1) https://www.siemensgamesa.com/en-int/products-and-services
(2) https://www.ge.com/renewableenergy/wind-energy
(3) https://www.vestas.com/en/products#!
(4) https://www.statkraft.com/about-statkraft/where-we-operate/norway/fosen-vind/
(5) https://www.vestas.com/en/media/~/media/6a227bee6eff4b9e84e11e28296305ba.ashx
Are you interested in hearing more about our services and products? Please follow our page on LinkedIn and contact us for further information.